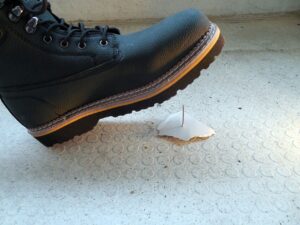
Accidents in the workplace are going to happen. Although contractors and their work crew spend long hours in classes to acquire safety certifications and even put ironclad protection methods into place, all the training and safe practices in the world do not account for human error. Somebody forgets to secure a stepladder. Someone else left out a crucial step in assembling scaffolding. Or an employee gets in a hurry with a genie lift. All of these things happen daily on work sites in various industries throughout the country. To help you better understand where the safety hotspots are and what can be done to minimize the chances of injury or death in your company, we’ve prepared a list of the top 10 most common on-the-job accidents and their leading causes. We have also provided some resources and tips on how to avoid them. Be safe!
1) Fall Protection
Failure to set proper protection in place in the event of a fall can result in catastrophe. According to a 2015 report, OSHA cited fall protection in construction as the leading standard violation that lead to injuries and fatalities among contracting businesses. There are two categories of fall protection:
- Prevention: Equipment is put in place to minimize or eliminate the possibility of fall. Some examples would include solid railing, wire rope railing, and harnesses.
- Training: Do your employees know how to set up barricades? Do they know how to wear safety harnesses? Have they been properly trained in all security measures?
2) Hazard Communication
Chemicals and toxic waste can lead to an array of injuries including poisoning and burns. OSHA standards require that contractors provide safety data sheets that are readily accessible to all workers. Employees are trained to identify toxic substances in the work area and widely communicate their existence to all other employees.
3) Scaffolding
Scaffolding accidents occur almost daily. Improper scaffolding structure, lack of thorough inspections, and falling objects are what usually leads to job-related accidents. Another factor leading to scaffolding accidents is that someone placed too much weight at the top. Crewmembers are on or around scaffolding throughout the day. For this reason, contractors and their team should never assume that once they correctly put a scaffold into place that it’s going to remain that way all day long. Inspections should be performed more than once during a work shift. It is also a good idea to have barriers set in place to keep tools and equipment from falling.
4) Respiratory Protection
The first thing to remember in protecting your crew from potential respiratory problems is that the right mask must be worn to protect from fumes. Educate yourself on which masks your workers will put on in a given situation. In some cases, dust may be the problem. In others, workers might have to contend with carbon monoxide or asbestos. Below is a list of the most common hazards:
- Mists
- Carbon Monoxide
- Asbestos
- Lead dust and fumes from welding-related jobs
- Silica Dust from concrete and sandblasting work
- Vapors that arise from paint-related work, solvents, and coatings
- Insulation particles and vapors such as fiberglass and spray foam
5) Lock and Tag Energy Hazards
Construction sites contain dangerous equipment and machinery. Machine maintenance is an ongoing issue. Before a team member can repair on-site equipment, it must be either locked out or tagged out. By doing so, a crewmember ensures that the equipment is safe to work on because it has been shut down and is no longer operable. The machinery is then rendered safe by the tags and the locks.
6) Forklifts and Other Powered Industrial Vehicles
Forklifts cause 80-90 deaths each year. In most of those cases, the operator was either using the forklift for the wrong kind of job or too much weight was applied to the lift causing either a driver or a co-worker to be crushed once the forklift tipped over. 90% of all forklifts made and used in the U.S. will fall prey to an accident. In almost every case, someone who was not trained or certified to operate the forklift caused the injury. For an employee to operate a forklift or similar powered industrial vehicle, three things need to happen:
- The operator is required to have a license.
- The operator must have proper training and certification.
- The operator must have permission from the employer.
7) Ladders
Companies in almost every field of the contracting and home improvement industry use ladders every day. Due to its unstable nature, there are strict safety codes set in place for a ladder’s use. Safety.BLR offers some practical do’s and don’ts of ladder safety:
- Do keep one hand on a side rail at all times.
- Do keep your body centered on the ladder. A good rule of thumb is to keep your belt buckle between the rails.
- Do keep your body straight and as close to the ladder as possible.
- Do move carefully and slowly when working on a ladder.
- Don’t lean too far in either direction. Overreaching is a leading cause of ladder accidents.
- Don’t reach too far overhead either. Use a taller ladder to reach higher, if necessary.
- Don’t try to reposition the ladder while you’re standing on it. Get down and move it.
8) Machine Guarding
Some operating equipment, while providing a valuable function to a company’s daily operation, is extremely dangerous to work around. Therefore, shields and barriers must be used to protect workers from eminent danger. On most construction sites, machine guarding is usually the first consideration when it comes safety. An example of this would be to set a temporary fence to keep a work crew at a safe distance from a large crane carrying heavy steel.
9) Electrical Wiring
Electrocution is the fourth leading cause of death among construction workers. The main issues: contact with live wiring, unprotected equipment, and, surprisingly, light fixtures. Roofing companies and other contracting companies where workers perform jobs that elevate them into high places were also hurt or killed by power lines. Failure to lock and tag all high-risk areas led employees to walk right into dangerous situations. In many instances, workers had no clue that that wiring they were about to touch was even live.
10) Electrical System Design
Sometimes injury or death in the workplace is not the fault of either the contractor or the crew. In some instances, it can be purchasing faulty electrical equipment or improper design of machinery that led to the problem. Most manufacturers of high-end construction machinery have a procedure for checking and double-checking the safety of the electrical system within the equipment. Occasionally, however, something can go wrong. Faulty electrical design can lead to fires, blasts, electrocution, or power failure during a critical moment when safety is of utmost importance. Daily equipment inspection is vital to the security of a job site. If any machinery or devices are found to be defective, it should be removed or tagged and locked immediately and kept away from all crewmembers. If someone has previously plugged the machinery into a power source, then the electrical supply needs to be cut off. They need to inform others that the equipment is faulty to avoid electrocution.Note: Much of information provided in this article comes directly from the Occupational Safety and Health Administration (OSHA) and can be reviewed on their site using the above links provided. If you are a startup contractor, the OSHA handbook should be something that you update and regularly read as the existing laws and regulations change annually.